إنتاج الصلب

المواد الفلزية المعروفة التي يطلق عليها الحديد والصلب هي في الواقع سبائك لعنصر الحديد، وبوجه عام فإن الصلب هو سبيكة من عنصرى الحديد والكربون. ولا تزيد نسبة الكربون فيها على 2% . وتحتوى معظم أنواع الصلب في الغالب بالإضافة إلى الكربون، على كمية من عنصر المنجنيز، كما يحتوى عدد من سبائك الصلب أيضا على عدد آخر من عناصر أخرى بجانب ما ذكر من عناصر. و تعتمد خواص اى نوع من أنواع الحديد والصلب إلى حد بعيد على التركيب الكيميائى للسبيكة. ويمكن ان تتغير هذه الخواص بدرجة ملحوظة بإجراء عمليات التسخين والتشكيل.
أنواع منتجات الحديد:
و على الرغم من وجود آلاف الأنواع المختلفة من الحديد والصلب، الا انه يمكن تقسيم أنواع الحديد إلى المجموعات التالية:
حديد التمساح: وهو الحديد الناتج من الفرن العالي؛ وتحتوي معظم أنواع حديد التمساح علي 93% حديد، ومن 3% إلى 4% كربون؛ بالاضافه الي كميات اقل من عناصر اخري. واصل مصطلح تماسيح الحديد يعود الي الطريقة التي اتبعت في عمليات صب مصهور الحديد الناتج من الفرن العالي خلال منظزمه من القوالب وضعت حول قناه مركزيه. ولقد أطلق علي القضبان الحديدية المتكونه داخل قالب الصب اسم التمساح. وفي الوقت الراهن يستخدم معظم خام حديد التمساح في حالته المنصهره في صناعه الصلب. وفي الوقت الراهن يستخدم معظم خام حديد التمساح في حالته المنصهره في صناعه الصلب، ولا يجري صبه في قوالب. ولكن كميه صغيره منه فقط تصب كما كان يحدث في السابق، وذلك لتصنيع حديد الزهر أو الحديد المطاوع.
الحديد الزهـر: وهو أي نوع من سبائك الحديد المحتويه علي نسبه عاليه من الكربون، حيث تتراوح نسبه الكربون فيهمن 2% الي 4% ، كما يحتوي علي السيليكون بنسب تتراوح من 1% الي 3% . ونظرا لارتفاع نسبه الكربون في الحديد الزهر، فأنه لا يمكن تشكيله وهو في حالته الجامده؛ مهما كانت درجه الحرارة التي سيُسَخَّن اليها. ويشكل الحديد الزهر في العديد من التطبيقات ما يتميز به من صلاده؛ وانخفاض في التكلفة، ومقدره عاليه علي امتصاص الصدمات. ولهذه الأسباب يعد الحديد الزهر ماده انشاءات مفيده ومهمه. الحديد المطاوع هو تقريبا حديد نقي مخلوط مع ماده تشبه الزجاج؛ وعلي العكس من حديد الزهر فان الحديد المطاوع قابل للطرق، ولهذا يمكن طرقه الي اشكال مختلفه، ويقاوم الحديد المطاوع التأكل (الصدأ) بصوره أفضل من مقاومه الحديد الزهر. ولقد كان الحديد المطاوع أحد الصور الحديدية التي استخدمت كثيرا في الماضي لانتاج كثير من المنتجات التجارية التي يجري تصنيعها حاليا من الصلب؛ وفي الوقت الراهن لا تنتج شركات الصلب الا كميات صغيره ومحدوده من الحديد المطاوع، ويستخدم معظمها في صناعه قضبان السكك الحديدية، والبويات وبعض أعمال الديكور والزخرفة
'أنواع منتجات الصلب :'
- الصلب الكربوني
- الصلب غير القابل للصدأ
- الصلب السبيكي
- صلب العدد
الصلب الكربوني: ويعد أكثر أنواع الصلب استخداما، وتعتمد خواصه اعتمادا كليا علي ما يحتويه من الكربون.[1][2] وتحتوي معظم أنواع الصلب الكربوني في الغالب علي نسبه كربون اقل من 1& . ويصنع الصلب الكربوني في صوره منتجات متعدده تسمل قضبان الإنشاءات واجسام السيارات ومعدات المطابخ والعلب
الصلب السبائكي: وهو الصلب المحتوي علي بعض الكربون، لكن خواصه تعتمد بصوره اساسيه علي العناصر الكيميائية الاخري المضافه للسبيكه؛ ويعمل كل عنصر من العناصر المضافه علي تحسين علي تحسين خاصيه واحده أو أكثر من خواص الصلب، وعلى سبيل المثال ن فان اضافه المنجنيز للصلب يزيد من صلادته ومتانته ومقاومته للبري، وتساعد اضافه النيكل علي رفع المتانة وبخاصه للصلب المستخدم عند درجات الحرارة شديده الانخفاض، ويعمل الموليبدينيوم علي رفع الصلادة وتحسين مقاومه الصلب المتاكل، بينما ترفع اضافه التنجستين من مقاومه الصلب للحراره، وعلاوه علي اضافه العناصر المذكورة الي الصلب فهناك عناصر اخري تضاف اليه وتشمل الالومينيوم والكروم والنحاس والسليكون والتيتانيوم والفاناديوم
الصلب غير القابل للصدأ: ويعد أفضل أنواع الصلب في مقاومه التاكل؛ ويعتبر الكروم العنصر الاساسي لسبيكه الصلب غير القابل للصدأ. وتحتوي جميع أنواع سبائك الصلب غير القابل للصدا علي 12% كروم علي الاقل، وترتفع هذه النسبة لتصل في بعض السبائك الي 30% ، كما تحتوي اعداد كبيره من سبائك الصلب غير القابل للصدأ أيضا علي عنصر النيكل، ويصنع من الصلب غير القابل للصدأ الكثير من الأدوات المنزلية مثل السكاكين والمعالق والاطباق والاوعيه والقدور؛ كما تستخدم الأنواع المختلفة من الصلب غير القابل للصدأ في إنتاج الكثير من المنتجات المهمة الاخري مثل اجزاء السيارات واجهزه المستشفيات والشفرات الحاده
صلب العُدد: ويعتبر اعلي جميع أنواع الصلب صلادة؛ فصلادته عاليه جدا، ويستخدم اساسا في صناعه وانتاج عدد تشكيل المواد الفلزيه، ويصنع صلب العدد من خلال المعالجه الحرارية لبعض الأنواع الخاصة من الصلب الكربوني أو الصلب السبائكي؛ وتجري المعالجة عن طريق تسخين الصلب الي درجه حراره عاليه، ثم تبريده في وسط تبريد معين (سواء زيت أو محلول ملحي أو ماء) بسرعه
'مصادر خام الحديد :' ويشير مصطلح خام الحديد في العادة، إلى صخر أو معدن يحتوى على كمية كافية من فلز الحديد تجعله مناسبا (عمليا واقتصاديا) لاجراء عملية التعدين. ففى بعض الأحيان، ريما يحول موقع ترسبات الحديد وبعض مواصفاتها دون استغلالها مصدرا لخام الحديد؛ لكن على الرغم من سوء الموقع وتدنى درجة الحديد إلا ان تحسن كل من وسائل النقل وتطور تقنية التعدين، وكذا تحسين عمليات تهيئة الخام وتهذيبه قد تؤدى في المستقبل إلى تحسن في خواص الترسبات الرديئة، وتحولها إلى ترسبات تجارية يمكن الاستفادة منها. كذلك يمكن ان تؤدى زيادة الطلب على الحديد وارتفاع استهلاكه وتغيير سياسات الحكومات؛ وكذا التبدل في ظروف التجارة الدولية، إلى البدء في استخدام مناجم خام حديد جديدة لم تكن اقتصادية في السابق. وتتوفر خامات الحديد ومصادره في العالم بكميات كبيرة، وذلك على الرغم من ان صناعة الصلب المستمرة تستهلك كميات ضخمة من مخزون هذه الخامات؛ ونتيجة لاستخدام خامات الحديد الغنية وقرب نفاذها، فقد طورت شركات صناعة الصلب تقنيات صناعية حديثة حتى يمكن استخدام خامات الحديد الفقيرة.
أولا مرحلة الشحن
[عدل]'الخردة'
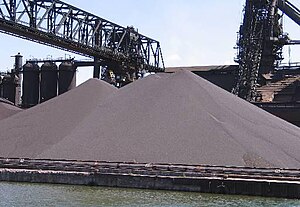
الخردة (scrap) مع أنها تعد مصدراً غنياً بالحديد لا يحتوى على شوائب وأكاسيد بنسبة كبيرة، إلا أنها تحتوي على نسبة مما يسمى بالـ (Tramp Elements) كالنحاس والقصدير والرصاص والزرنيخ.... كما يعيب الخردة عدم التجكم في التركيب الكيميائي للشحنة، فقد تكون الخردة مجهولة الهوية من حيث التركيب الكيميائي، وهذا له مخاطرة الكثيرة. و للخردة تصنيفات متعددة: فمنها الخردة الخفيفة والثقيلة، ومنها المختلطة مع الجلخ Slag Mixو المرتجعة كمنتجات معيبة Home Return، وخردة الحرب وغيرها، لذا يجب أن تمر الخردة بمراحل فرز وإعداد جيدة قبل شحنها في الفرن، وذلك لإزالة أي شوائب غريبة قد تضر بالفرن أو بعملية الإنتاج أو جودة المنتج كالمواد العازلة (الخشب والبلاستيك والكاوتشوك...) وكذلك الخردة كبيرة الحجم والطويلة بشكل غير ملائم لشحن السلة بالفرن (يجب تقطيعها بشكل ملائم أولاً قبل شحنها) والمواد الضارة بحراريات الفرن (كالرصاص والرمل...) والمؤثرة على تركيب المنتج النهائي (كالنحاس والفسفور والكبريت...) وكذلك المواد القابلة للانفجار (كالقنابل والذخيرة والأوعيى المغلقة كأنابيب الغاز والتي يجب فتحها وتقطيعها أولاً).
الاعتبارات التي يجب مراعاتها عند تصميم السلة الخاصة بشحن الفرن:
- ألا تزيد النسبة بين حجمن السلة وحجم الغلاف المعدني للفرن عن 85%.
- ألا تزيد النسبة بين قطر السلة وقطر الفرن عن 90%، وذلك لتجنب سقوط الخردة خارج الفرن أثناء عملية الشحن.
- كلما قل عدد مرات الشحن لكل صبة/ فإن زمن تعطل الفرن للشحن يصبح أقل، كما أن الفقد الحراري أثناء فتح وغلق سقف الفرن يصبح أقل.
الحديد المختزل بالطريقة المباشرة: و يشار إليه بالرمز (Direct Reduced Iron –DRI)، و يُحَصَّلُ عليه عن طريق إستكمال عملية اختزال كرات أكسيد الحديد (Oxide Pellets) بتمرير الميثان أو الغاز الطبيعي (CH4) عليها في درجات حرارة ما بين (950-1050) درجة مئوية خلال أفران معينة من شهرها فرن "مدركس (MIDREX)"، هذا الغاز الطبيعي يمثل مصدر الكربون اللازم لعملية اختزال الخام في صورته الصلبة المباشرة دون صهره؛ (لذلك تسمى تلك الطريقة بطريقة الاختزال المباشر). و عملية الاختزال ما هي إلا تقليل أو (اختزال) لنسبة الاكسجين داخل خام أكسيد الحديد؛ وبالتالي زيادة نسبة الحديد أو التمعدن على حساب ذلك، وذلك عن طريق وجود عامل مختزل، عبارة عن خليط من الغازات (الهيدروجين وأول وثاني أكسيد الكربون)، تقوم بالإتحاد مع هذا الاكسجين مستهلكة إياه، وتحويله مع من أكسجين متحد مع الحديد (أكسيد حديد)؛ إلى أكسجين ولكن متحد مع هذا العامل المختزل تاركة الحديد في شكل حر و الحديد الناتج عبارة عن مكورات حدبد تسمى بالحديد الإسفنجي، ولكي يكون الحدي الإسفنجي مناسب لفرن القوس الكهربي؛ يجب أن تتوافر فيه الشروط الآتية:
- حجم الحبيبات يتراوح من 9 مم إلى 16 مم.
- نسبة الحديد لا تقل عن 84%.
- نسبة الكربون لا تقل عن 1.2%.
و يتم نغدية الـ (DRI) إلى مصنع الصلب بصورة مستمرة عن طريق سيور خاصة قادمة من مصانع الاختزال المباشر، ثم يُخَزَّن في صوامع (Silos)؛ ثم ينتقل منها بسيور أخرى إلى مصنع الصلب ليُغَذَّى عن طريق الـ (Chuter) إلى فتحة التغذية الموجودة بسقف الفرن القوس الكهربي. كما يُشْحَنُ الـ (DRI) خلال السلة التي تُشْحَنُ بالفرن في بداية إنتاج الصبة. جدير بالذكر أن استخدام الـ (DRI) كمصدر للحديد في صناعة الصلب له الكثير من المزايا، كفارق السعر عن الخردة؛ وسهولة تغذيته في الفرن بصورة مستمرة، بما يوفر زمن فتح وغلق الفرن أثناء الشحن (مقارنة بشحن الخردة بالسلات)، وكذلك الفقد الحراري الناتج عن ذلك، وكذلك التحكم والمعرفة الدقيقة للتركيب الكيميائي والخواص الفيزيائية للشحنة، ولكن على الجانب الآخر له بعض العيوب؛ والتي من أهمها احتواؤه على الشوائب والمركبات الأكسيدية (كالكبريت والفسفور وأكسيد السليكون والمنجنيز وغيرها)؛ والتي يطلق عليها الـ (Gangue Materials) الأمر الذي يسبب مشاكل كبيرة منها زيادة الطاقة المستهلكة في صهر هذه المكونات، بالإضافة إلى الضرر الناشئ عن وجود هذه المكونات على حراريات الأفران والبواتق.
و بفضل استخدام الـ DRI كمصدر للشحنة المعدنية في حالة إنتاج أنواع الصلب النظيف (و الذي يطلق عليه Clean Steel)، نظراً لما يلي
- لاحتوائه على نسبة منخفضة من الـ Tramp Elements كالرصاص والنحاس والزنك والكروم والنيكل والموليبدنيوم....إلخ.
- لاحتوائه على نسبة كربون حوالى (3-5%) الأمر الذي يساعد في تكوين ما يسمى بالخبث الفوار أو الرغوى، والذي يعتبر من أهم مميزاته تنقيه المصهور المعدني من الشوائب والمتخللات غير المعدنية (n.m.i).
- ولكن يعيب الـ DRI انخفاض درجة التمعدن مقارنة بالخردة، حيث تكون (92-95%) فقط، مع وجود نسبة عالية من الأكاسيد (كأسيد السيليكون والألومنيوم والكالسيوم...إلخ)، وهذا يعني:
- انخفاض عائد الصب.
- زيادة مقدار الطاقة والزمن اللازمين للصهر مقارنة بالخردة.
- زيادة معدل إستهلاك الإلكترودات والحراريات الخاصة بالفرن.
و يتراوح قطر كرات الـ DRI ما بين (9 - 16مم)، أما الكرات ذات القطر الأقل من 3 مم فيطلق عليها Fine، وليست Pellets، أما الكثافة
- المطلوبة فهي ما بين (1.6-1.9 طن/ م3)/ ويثم شحن الفرن بالـ DRI بطريقتين:
- عن طريق السلة، ذلك بشرط ألا تزيد نسبته من محتويات شحنة السلة عن (20-30%).
- عن طريق التغذية المستمرة، ويراعى في هذه الطريقة ما يلي:
- ترك مسافة مرتفعة بدرجة كافية للتغذية؛ لإعطاء فرصة لكرات الـ DRI لاختراق طبقة الخبث بفعل الجاذبية.
- أن تبدأ التغذية بعد وصول درجة المصهور المعدني إلى (1580 مئوية).
- أن تبدأ التغذية بعد تمام انصهار الخردة داخل الفرن.
- أن يكون معدل التغذية في البداية حوالي (7-10 كجم/ دقيقة ميجاوات).
- معدل التغذية القياسي للـ DRI ما بين (25-30 كجم/ دقيقة ميجاوات).
- أن تتم التغذية بالتواكب مع التغذية بالـ DRI.
مثال توضيحي: إذا كان معدل الطاقة الكهربائية 107 (ميجاوات)، وكان معدل التغذية القياسي هو (28 كجم/ دقيقة ميجاوات)، فإن معدل التغذية المطلوب يكون:
107 (ميجاوات) x 28 (كجم/ دقيقة ميجاوات) ≈ 3000 كجم/ دقيقة 3000 كجم/ دقيقة x (60/ 1000) = 180 طن / ساعة
فإذا قل معدل الطاقة عن هذه القيمة (أو زاد معدل التغذية عن القيمة المبينة بالمثال)، فإنه يحتمل تكوين مناطق متجمدة من الشحنة المتجمدة (و تسمى بالـ Ice Berg) بالفرن. أما إذا حدث العكس (زيادة معدل الطاقة أو نقص معدل التغذية)، فإن درجة حرارة المصهور المعدني تصبح أعلى من المطلوبن وهذا يعني:
- إستهلاك زائد في الطاقة الكهربائية.
- إستهلاك الإلكترودات وحراريات زائد
الاعتبارات التي يجب مراعاتها عند تغذية الفرن بالـ DRI: أفضل موضع يُغَذَّى الـDRI من خلاله هو منتصف الدائرة المارة بمراكز الإلكترودات الثلاثة/ وتسمى بالـ (Electrode Pitch Circle). أثناء عملية التغذية بالـ DRI، يتم التغيل على جهد كهربي منخفض وتيار كهربي عالي، وهذا يعطي ما يسمى بالقوس الكهربي القصير Short Arc. نظراً لزيادة مساحة سطوح كرات الـ DRI، فإن: فرصة تأكسده في الجو المكشوف تكون كبيرة، خصوصاً في مدى درجات حرارة (210- 275 مئوية)، وهذا أيضاً يعد فقد في عائد الشحنة المعدنية. فرصة اشتعاله تكون كبيرة، ولذا فإن معظم أنظمة مناولة الـ DRI كالسيور وغيرها، تكون مزوده بأنظمة مكافحة الحرائق.
الحديد الغفل Pig Iron: و يمتاز الحديد الغفل بأنه ذو كثافة عالية، وبالتالي يشغل حيزاً صغيراً من السلة أثناء شحنه بها، لذبك يمتاز بسهولة الشحن، كما أنه يحتوي على نسب عالية نسبياً من الكربون (من 3- 5%)، والسيليكون (حتى 2%)، والمنجنيز (حتى 1%)، وهي العناصر التي تُسْتَغَلُ في تفاعلات الأكسدة (و هي تفاعلات طاردة للحرارة Exothermic Reactions)/ والتي تسهل عملية الصهر داخل الفرن، وتوفر في إستهلاك الطاقة الكهربية المستخدمة في الصهر، ويحتاج طن الحديد الغفل حوالى (280 كيلو وات ساعة) لصهره، أي أنه أسهل بكثير في صهره مقارنة بالـ DRI أو الخردة.
المواد الثانوية (Sub-Materials)
[عدل]و تسمى أحياناً بالإضافات (Additives) وتظهر أيضاً في تركيب المنتج النهائي في صورة عناصر سبائكية (كالكربون والمنجنيز والسيليكون والفانديوم....)، كما أنها تساعد على سهولة أداء عملية الإنتاج وتساهم في مدى جودة المنتج النهائي (من حيث تجانس تركيبه ونقاؤه من الشوائب وخواصه الميكانيكية والكيميائية وغيرها...)، ومنها ما يلي:
اولا الكوك
واضافه الكوك لا يكون الغرض منها الحصول على نسبه معينه للكربون في المنتج النهائى فحسب، ولكن وجود الكربون له فوائد أخرى: فالكربون يعتبر عامل مختزل بمعنى أنه بقلل نسبة الاكسجين في المعدن بحيث يتحد مع الاكسجين الموجود بالمعدن ويكون فقاعات من أول أكسيد الكربون والتي تتصاعد خلال مصهور المعدن وتطفو حتى تخترق طبقة الخبث محدثه تأثير التقليب أثناء صعودها؟، وتأثير الفوارن أثناء اختراقها لطبقة الخبث والذي يسبب ظاهرة الخبث الرغوى أو فوارن الجلخ والتي تعتبر من أهم الظواهر التي تحسن من أداء عملية أنتاج الصلب. وتتنوع طرق شحن الكوك على حسب حجم حبيباته، والتي تعتمد على الغرض من أضافتها ومكان أضافتها سواء في السلة أو خلال فرن البوتقة أو أثناء الصب، وهناك ثلاثة أشكال للكوك المستخدم بمصنع الصلب، تختلف حسب حجم حبيبات كل منها كالتالى: 3-15 مم: ويسمى بكوك لامب ويُشْحَن خلال السلة عن طريق الونش الكباش 0.5 – 3 مم: ويسمى بكوك باودر ويُشْحَن أو يُحْقَن أثناء عملية التشغيل عن طريق مضخات والتي تثبت في جوانب الفرن تمامم مثل مضخات حقن الاكسجين.
ثانياً الجير المحروق (أكسيد الكالسيوم)
ويضاف أثناء شحن السلة في بداية الصبه، كما يضاف التابنج عن طريق الكاتر واثناء المعالجة في فرن البوتقة على حسب الطلب، وإضافة الجير المحروق الغرض الاساسى منها المحافظة على قاعدية الخبث وهي حاصل قسمة وزن الاكاسيد القاعديه وعلى رأسها اكسيد الكالسيوم على الاكاسيد الحامضيه وعلى رأسها ثانى أكسيد السيلكون في الخبث، ويفضل أن لاتقل القاعديه 2, وخلال وذلك بغرض الحفاظ على الحراريات من التآكل، وذلك لأن: التآكل الكميائى الحادث للموادالحراريه غالبا مايكون في منطقة الخبث وذلك لوجود بعض الاكاسيد الحامضيه في التركيب الكميائى للخبث وعلى رأسها السيليكا، هذه الاكاسيد الحامضيه تتفاعل بشراهه مع المكونات القاعديه لمواد التبطين الحرارية والتي تكون غالبا أكاسيد قاعديه كالماغنيسيا وذلك بغرض تحقيق التشبع الكافى للخبث من المكونات القاعديه، فيضطر لتحقيق هذا التشبع بالحصول عليه من مكونات البطانه الحرارية القاعديه . وللحد من هذه العملية، نقوم باضافة الجير المحروق واحيانا الماغنيسيا وهي أكاسيد قاعديه بحيث تعتبر كامداد للخبث باحتياجاته من الأكاسيد القاعديه ليحقق هذا التشبع دون الحاجة إلى انتزاعها من البطانه الحرارية، أو بمعنى آخر: شراهة السيليكا للتفاعل مع الجير المضاف أعلى من شراهتها للتفاعل مع مكونات البطانه الحرارية وبالتالى تأخذ كفايتها من المكونات القاعديه بالتفاعل مع الجير المضاف أولا، تاركه بذلك مكونات البطانه الحرارية دون أن تتفاعل معها . وأغلب تفاعلات التآكل الحادثة في الحراريات تتم خلال أوقات الانتظار خصوصا بعد الصب من الفرن في البوتقة الكبيرة وقبل المعالجة في فرن البوتقة، لذلك يضاف الجير أثناء صب الفرن عن طريق القاطععلى سطح الصبه بحيث يتفاعل بشكل مباشر مع طبقة الخبث للحد من هذه التفاعلات خصوصا أثناء وقت الانتظار. وعلى الجانب الآخر نجد أن أضافة الجير بالرغم من أنها تزيد من قاعدية الخبث، فأنها تزيد تزيد من لزوجة الخبث بشكل واضح، وهذا له بعض الآثار السلبية على سير العملية
ولكن هل يمكن استخدام الحجر الجيرى بدلا من الجير المحروق ؟ الحجر الجيرى عباره عن كربونات الكالسيوم، أما الجير المحروق فهو عباره عن أكسيد كالسيوم ومن ذلك يتضح أن المادة الخام للجير المحروق هي الحجر الجيرى، والذى يُحَصَّل عليه من الصخور في الطبيعة ثم يجرى عليه عمليات الاستخراج والمعالجة المبدئيه كالتكسير والطحن والتركيز بطرق الفصل والتركيز المتنوعة، ثم يجرى عليه عمليه تسمى بالكلسنه، وهي عملية تحليل حرارى للحجر الجيرى لتركيز نسبة عنصر الكالسيوم بداخله على حساب تقليل تركيزات الاكسجين
وذلك بتسخين الحجر الجيرى بطريقه معينه من خلال أفران الكلسنه، عند درجة حراره من 900 ل 1000 درجه مئويه يؤدى ذلك إلى تحلل الحجر الجيرى وتصاعد غاز ثانى أكسيد الكربون، وتزايد تركيز أكسيد الكالسيوم إلى الضعف تقريبا بمعنى أننا أذا احتجنا في الظروف العادية للتشغيل إلى كمية حجر جيرى مقدارها 2 طن، فأنه يمكن الحصول على نفس التأثير باضافة نصف الكميه فقط من الجير المحروق اى طن واحد فقط .وهذا بالطبع يعطى المزايا الآتيه:
- تقليل كميات غاز ثانى أكسيد الكربون المتصاعده خلال تحلل الحجر الجير
- تقليل الطاقة الكهربية المستهلكه الازمه لتحلل الحجر الجيرى داخل الفرن
- تقليل الفقد الحرارى المستهلك خلال تحلل الحجر الجيرى، وبالتالى فرصة حدوث انخفاض للحراره، وذلك نتيجة تقليل الكميه المضافه إلى النصف فقط .
ويلاحظ أنه أذا احتوى المعدن المصهور على نسبه كبيره من الفوسفور فأنه يفضل في هذه الحالة أضافة الحجر الجيرى وذلك لما له من تأثير انخفاض الحرارة بحيث يقلل من درجة الحرارة حتى تتلائم مع ظروف ازالة الفوسفور، كما أن تحلل أو كلسنة الحجر الجيرى خلال الفرن تساعد على زيادة كميات الغازات المتصاعده بما يساعد في عملية التقليب والخلط بين المعدن المصهور والخبث . أما إذا زادت درجة الحرارة عن 1580 درجه مئويه، فيمكن في هذه الحالة أضافة كميه اضافيه من ال دى ار اى أو الخردة لتقليل درجة حرارة المعدن مره آخرى، لتتلائم مع الدرجة المثلى لحدوث عملية أزالة الفوسفور، ولمنع رجوع أو ترسيب الفوسفور المتأكسد مره آخرى بالمعدن . يجدر الإشارة هنا إلى أهمية ازالة الفوسفور والكبريت من الصلب المنتج قدر الإمكان، نظرا لما يسببه كلاهما من تأثيرات سلبيه على خواص الصلب، فالكبريت يسبب ظاهره تسمى بالتقصف على الساخن حيث يتقصف الصلب المنتج أثناء عملية درفلته على الساخن، وذلك نتيجة وجود كبريتيد الحديد داخل التركيب البنائى لهذا الصلب والتي تكون مركبا كميائيا مع الحديد عند درجات حراره من 930 وحتى 1260 درجه مئويه، هذا المركب المتكون له درجة انصهار منخفضه وبالتالى يتكسر أثناء الدرفله ويسبب هذا التقصف، أما الفوسفور فيسبب ظاهره تسمى بالتقصف على البارد حيث يتقصف الصلب المنتج أثناء عملية درفلته على البارد وذلك نتيجة وجود أكاسيد الفوسفور داخل التركيب البنائى لهذا الصلب وله نفس التأثير السابق شرحه على الكبريت ولكن عند مدى درجات حرارة الدرفله على البارد .
ثالثا: الفلوروسبار (فلوريد الكالسيوم)
يضاف الفلوروسبار في فرن البوتقة بغرض تحسين سيولة الخبث عن طريق تقليل درجة انصهار الوسط وبالتالى تحسين عملية تفاعل الخبث بالمعدن؛ وبالتالى يتحسن التفاعل الحادث بينهما، بما يحسن من درجة نقاوة المعدن وازالة المتخللات غير المعدنية الموجودة به، وكذلك تحسين عملية صهر ومعالجة المعدن والخبث . فوجود خبث ذو كثافه منخفضه ولزوجه عاليه نتيجة أضافة الجير المحروق وزيادة القاعدية، كل هذا يؤدى لانحباس كميات كبيرة من الغازات الموجودة بالمعدن تحت طبقة الخبث، ومع استمرار زيادة كمية هذه الغازات فأنها تخترق طبقة الخبث أو ترفعها لأعلى وتسبب حدوث فوران شديد بفرن البوتقة أثناء التشغيل . ولكن لاحظ أن الفلوروسبار يحتوى على نسبة من السيليكا وهو أكسيد حامضى يسبب تآكل الحراريات القاعدية كما ذكرنا قد تصل إلى 5 بالمائه، وبالتالى لا يتم استخدام الفلوروسبار الا عند الضرورة في حالة زيادة لزوجة الخبث بدرجة كبيرة وبكمية لا تزيد عن 20 كجم /صبه .
رابعا: الفيروسيليكون والسليكون منجنيز والألومنيوم :
ويضاف الفيروسيليكون في فرن البوتقة بغرض أختزال أو أزالة الأكسجين من الصبه؛ كما يعتبر مصدر للسيليكون كعنصر سبائكى في الصلب المنتج وفي حالة التعامل مع الصبات وكذلك الصبات التي لها مدى ضيق لنسبة السيليكون؛ فاننا نستخدم الألمونيوم في أضيق الحدود كعامل مختزل مع خنق التقليب وإضافة كميه من الجير بغرض رفع لزوجة الخبث بحيث يتعامل الألمونيوم المضاف مع طبقة الخبث فقط دون أن يهبط خلال المعدن لأن وجود الألمونيوم في المعدن مع أجراء عملية الصب المستمر في جو مفتوح يؤدى لحدوث شروخ نتيجة تفاعل أكسيجين الهواء الجوى مع الألومنيوم وتكوين الألومينا
خامسا: الفيرو منجنيز:
ويستخدم كمصدر لضبط نسبة المنجنيز في المعدن خلال فرن البوتقة، ولا يستخدم الفيرو منجنيز كعامل مختزل للأكسيجين من الصبه لأن الأختزال يحتاج إلى كميات كبيرة منه وبالتالى أضافة هذه الكمية تسبب حدوث انخفاض في درجة الحرارة .
الطاقة المستخدمة
[عدل]'الطاقة المستخدمة' و في تلك المرحلة يتم صهر الشحنة داخل فرن القوس الكهربي بمساعدة نوعين من الطاقة الأولى : الطاقة الكهربية المستمدة من المصدر الكهربي ثلاثي القطبية الثانية : الطاقة الكيميائية الناتجة أو المنبعثة من تفاعلات الأكسدة الطاردة للحرارة والتي تحدث داخل الفرن
أولاً الطاقة الكهربية
حيث يتم إمداد فرن القوس الكهربي بمصدر كهربي ثلاثي الأقطاب عالى الجهد الكهربي ومنخفض التيار وهذا لتقليل مقدار الفقد في الطاقة قدر الإمكان. و يتم إمداد الطاقة الكهربية إلى الفرن خلال عدة خطوات حيث نحصل على الطاقة من مصدر الطاقة الرئيسي وهو محطة الطاقة وعن طريق الكابلات تنتقل الطاقة إلى المحول الكهربي الخاص بالفرن وهذا المحول يكون عبارة عن ملفين (ابتدائي وثانوي) ويتم التحكم في قيمة الطاقة الداخلة للملف الابتدائي عن طريق التحكم في عدد لفاته عن طريق ريوستات وبذلك يتم التحكم في قيمة الجهد على طرفي الملف الثانوي والتيار المار : NpVs = Ns Vp

ثم تنتقل الطاقة إلى الألكترودات، ونلاحظ أنه في نظام تشغيل الفرن كهربياً أنه يتم التشغيل عن طريق قوس قصير في بداية الصبة في مرحلة الغمس وكذلك في المرحلة النهائية من الصبة والتي تسمى مرحلى التنقية وهذا يقلل من أستهلاك الألكترودات ويتم عملية الصهر بكل سهولة ويسر و لكن إذا صحب ذلك وجود قطع خردة كبيرة فإن يعرض خزن التبريد والمكونات الأخرى في الفرن لأخطار الطرطشة بالأضافة لزيادة زمن الأعطال والذي يلزم لأصلاح هذه التلفيات عن طريق لحامها أو تغييرها أما في مرحلة الصهر فيتم التشغيل عن طريق قوس كهربي طويل والذي يتميز بمعدل تآكل أقل للحراريات.
ثانياً الطاقة الكيميائية
و هي الطاقة المتولدة عن التفاعلات الكيميائية الطاردة للحرارة وغالبا ما تكون تفاعلات الأكسدة وهذه الحرارة تساعد بشكل كبير في صهر الشحنة المعدنية وعلميات التنقية ومن أشهر التفاعلات هو تفاعل الأكسجين مع الكربون والذي تولد عنه نواتج غازية عبارة عن أول أكسيد الكربون والذي بدوره يساعد في تكوين الخبث الفوار أو الرغوي والذي يحسن بشكل كبير من ظروف عمليتي الصهر والتنقية كما يحافظ على حراريات الفرن ويقلل من معدلات استهلاك الألكترودات كذلك. و للحصول لعى هذا النوع من التفاعلات ؛ هناك طريقتان للإمداد بالكربون والأكسجين :
الأولى أستخدام المواقد: ويتم عن طريقها حقن الكربون والأكسجين، واستغلال الطاقة الحرارية المتولدة عن التفاعل الكيميائي بينما في صهر الشحنة المعدنية التي تكون في طريق تيار الأكسجين الخارج من الحواقن، وبالتالي تكوين فراغ كافي لأتمام عملية حقن الأكسجين بسلام، مع تجنب أرتداد تيار الأكسجين والذي له تأثيراً تدميريا على جسم تجهيز الحواقن نفسها وعلى خزن التبريد وجسم الفرن كذلك.
الثانية أستخدام نظام الحقن : و هذا النظام يلي تشغيل نظام الواقد خلال عملية التشغيل وهو يحقق حرارة تنتج عن تفاعل الأتراق بالأكسجين تسهم في عملية صهر الخردة وكما أن لهذه التفاعلات لها نواتج غازية وهي أول وثاني أكسيد الكربون وهي تساعد في تكوين الخبث الفوار أو الرغوي كما أن الأكسجين المحقون قد يستخدم في أكسدة بعض العناصر غير المرغوب فيها أو ضبط نسبتها في مصهور الصبة وذلك أثناء مرحلة التنقية.
ثانياً خطوات الصهر
[عدل]الخطوة الأولى

و هي مرحلة يتم فيها صهر بعض الحفر على سطح الشحنة الصلبة بحيث تمكن الألكترود من أختراق السطح الصلب للشحنة المعدنية بسلام ويحدث خلالها اقتراب للإلكترود من سطح الشحنة وبذلك يتولد القوس الكهربي والذي يكون ذو خطورة شديدة ويسبب اهتزاز شديد للفرن ومكوناته والغرض من هذه الخطوة هو صهر الخردة التي أسفل الإلكترودات مباشرة وبالتالي يحدث انغماس للإلكترودات لأسفل. في هذه المرحلة يتم تشغيل المحول الكهربي بحد أقصى 60% فقط من الطاقة الفعالة له وذلك بغرض الحصول على ظاقصى قدر ممكن من قيمة التيار وبالتالي الحصول على قوس كهربي قصير وذلك كله بغرض تقليل أي امكانية لتدمير خزن تبريد السقف والذي قد يحدث نتيجة أنعكاس أي قوس كهربي في أتجاه الخزان وتستمر تلك المرحلة حتى يحدث انغماس للإلكترودات خلال الشحنة المعدنية اللصلبة بشكل كافي.
الخطوة الثانية و هي مرحلة الصهر الرئيسية ويتم فيها رفع درجة حرارة الشحنة عن طريق الطاقة الكهربية وفي هذه المرحلة يتم تشغيل المحول الكهربي بالحد الأقصى له وبالتالي الحصول على قوس كهربي طويل وذلك بغرض الحصول على اعلى معدل صهر في اقل زمن ممكن، كما أننا نحتاج إلى القوس الكهربي الطويل لصهر اجزاء الشحنة المعدنية البعيدة عن الألكترودات والأجزاء الموجودة في الجوانب البعيدة من الفرن والتي لم يتم صهرها في الخطوة السابقة. و تدريجيا تزداد درجة تجانس عملية الصهر بحيث نحصل على أنصهار كامل للشحنة في كل من الجوانب البعيدة وفي المنتصف وهنا يمكن التقليل التدريجي في طول القوس الكهربي
الخطوة الثالثة و هي مرحلة التنقية حيث يتم تشغيل المحول الكهربي على 70-80 % فقط من الطاقة الفعالة وذلك بغرض الحصول على أقصى قدر ممكن من قيمة التيار وبالتالي الحصول على قوس كهربي قصير وذلك لأننا نحتاج إلى زمن كافي لإتمام عملية التنقية.
ميكانيكية التعامل مع الخبث الفوار
[عدل]الخبث هو منتج ثانوي يتكون اثناء صناعة الصلب عن طريق إضافة الجير المحروق وبعض الاضافات الأخرى خلال فرن القوس الكهربي ونتيجة لأنخفاض كثافته لإانه يطفو فوق سطح المصهور المعدني ويكون الخبث بمثابة مركب أسفنجني يمتص الأكاسيد المتكونة من مصهور المعدن وهذا يساعد بشكل كبير في عملية تنقية المصهور المعدني من الاكاسيد والشوائب والحصول على صلب ذو درجة نقاوة عالية بالشكل المطلوب والخردة الجيدة واتي تكون خالية من الشوائب والاتربة لا تتطلب ظاضافة كمية كبيرة من الجير وبالتالي تكون ذات أستهلاكات اقل للطاقة.
مزايا الخبث الفوار : عملية تكون الخبث الفوار تعتبر أحد أهم الخطوات الخاصة بصناعة الصلب عن طريق افران القوس الكهربي وذلك لأانه يوفر عدة مزايا : أمتصاص الإشعاع الناشئ عن القوس الكهربي وهذا يعني معدل أستهلاك طاقة أقل وحماية اعلى لخزن التبريد والحراريات و زيادة متوسط طاقة التشغيل وهذا بدوره يساعد على استغلال أقصى طاقة ممكنة للمحول الكهربي و تقليب أسرع للمعدن والخبث وهذا يعني زيادة معدل التنقية وصهر أسرع للخردة وتجانس كيميائي وحراري عالي و نتيجة لكل ذلك ؛ تحسين ناتج المصهور المعدني وبالتالي رفع قيمة العائد عن طريق التخلص من نسبة عالية من أكاسيد الحديد.
ثالثاً: مرحلة التقنية
[عدل]في بداية التقنية من المهم جداً أخذ عينة من المصهور لإجراء التحليل الكيميائى له، وتؤخذ هذه العينة عند درجة حرارة من 1570 إلى 1580 مئوية، ويجب الالتزام بالتعليمات القياسية لطريقة أخذ العينة ووقت أخذها والموضوع الذي تؤخذ منه، وذلك لضمان صحة التحليل الكيميائى وكون العين ممثلة للوضع الحقيقى للمعدن المنصهر، كما أن العينة تعتبر مؤشر جيد للتركيب النهائى للمعدن، ويتبين منها هل هناك حاجة إلى أي متطلبات أخرى إضافية (كإزالة الكربون أو الفسفور أو الأكسجين)....إلخ. وهناك عناصر لا يمكن إزالتها من المعدن (إلا عن طريق التخفيف والتخليط مع صبات أخرى)، ومن أشهرها النحاس والكوبالت والنيكل، وبالتالى يجب إزالة هذه العناصر من الشحنة المعدنية قبل عملية الشحن. وعملية إزالة العناصر بالأكسدة قد تتم خلال طبقة الخبث، أو عن طريق تفاعل الأكسجين مباشرة مع العنصر في المعدن وذلك يمكن التحكم فيه من خلال ضبط زاوية حقن الأكسجين ومسافة الحاقن وضغط الحقن بالقدر المناسب لإتمام ذلك، وإلا فإن الأكسجين المحقون سوف يفقد خلال جو الفرن أو خلال طبقة الخبث.
أولا: إزالة الفسفور:
ووجود الفسفور في تركيب الصلب يزيد من قوة تحمله ومن قابليته للتشغيل على ماكينات التشغيل (كالمخرطة والمقشطة والفريزة...إلخ)، لذا تكون نسبة عالية إلى حد ما في ال Free Cutting Steel، ولكن على الجانب فإن الفسفور يقلل من مقاومة الصلب للصدمات ومن قابليته للسحب والطرق، لذا يتم إزالة الفسفور من المعدن
وفيما يلى الظروف القياسية لإزالة الفسفور بكفاءة من المصهور المعدن:
- درجة حرارة المعدن ما بين (1540) وحتى (1580) مئوية: فتفاعل إزالة الفسفور الأساسى يكون طارد للحرارة، ولذلك فإن ارتفاع الحرارة عن هذا المدى قد يؤدى إلى سير التفاعل في الإتجاه العكسى (بمعنى ترسيب الفسفور وليس إزالته).
- توفير جو مؤكسد، بمعنى وجود جو غنى بالأكسجين سواء في صورته الحرة [O] ذائباً في المعدن، أو في صورة FeO في الخبث، لذلك فإن حقن الأكسجين وكذلك التفاعل الحيد بين الخبيث والمعدن يساعد في إزالة الفسفور من المعدن بكفاءة، وأفضل نسبة لل FeO في الخبث من 10 إلى 15% بحد أقصى، فزيادته عن 15% تقلل من لزوجة الخبيث وتقلل من عائد المعدن.
- خبث ذو قاعدية تتراوح من 2.2 وحتى 2.5 وذو درجو لزوجة معتدلة.
- اتصال جيد بين طبقة الخبث ومصهور المعدن، ويمكن تحقيق ذلك بمساعدة الخبث الفوار نتيجة تكوين فقاعات ال CO التي تسمح بمساحات اتصال أكبر بين الخبث والمعدن وكذلك تسمح بتحقيق عملية التقليب الجيد بين الخبث والمعدن.
- التجليخ المستمر، والذي يقلل من فرصة ارتداد الفسفور وترسيبه مرة أخرى من الخبث إلى المعدن، وخصوصا عند تشبع الخبث بكميات من P2O5CaO .
ثانياً: إزالة السيليكون:
وتفاعل أكسدة أو إزالة السيليكون طارد للحرارة، ونحصل عليه عن طريق الأكسجين المتواجد في جو الفرن، والأكسجين الذي قد يصل في حالة استخدام خام الحديد Iron Ore في الشحنة المعدنية (حيث يحتوى على نسبة أكاسيد عالية)، ولكن لا يفضل ذلك لما يلى:
- إضافة خام الحديد في الفرن تزيد من كميات الشوائب، وهذا يؤدى لزيادة الطاقة المستهلكة والزمن اللازم للتقنية.
- خام الحديد يحتاج إلى طاقة أكبر في صهره.
ولأن تفاعل إزالة السيليكون طارد للحرارة، فإنه يساعد في عملية الصهر ويقلل من زمنه وبالتالى يقلل من الطاقة الكهربية المستهلكة. ومن خلال المعادلات السابقة نجد أن كل كجم من السيليكون يحتاج في إزالته إلى 0.8 نيوتن م3 من الأكسجين، بمعنى أننا نحتاج (نظريا) إلى 0.08 نيوتن م3 أكسجين لإزالة 0.01% سيليكون من المعدن ، ولكن كفاءة هذه العملية تكون حوالى 80% فقط ، كما أن كفاءة التفاعلات تتأثر بخواص الأكسجين المحقون (كمعدل التدفق وضغط الحقن (لا يزيد عن 8 بار) وكذلك زاوية الحق). ولاحظ أن الخردة عالية السيليكون قد تعطى تأثيرا سلبيا على إزالة الفسفور، وذلط لأن :
- تفاعل إزالة الفسفور طارد للحرارة وبالتالى يرفع درجة حرارة المعدن وبالتالى يقلل من معدل إزالة الفسفور.
- تفاعل إزالة السليكون ينتج عنه زيادة كمية السيليكا في الخبيث، وزيادة السيليكا (وهي مركب حامضى) تقلل من قاعدية الخبث، وهذا يعاكس ظروف إزالة الفسفور.
- السيليكون له قابلية أعلى من الفسفور للتفاعل مع الأكسجين، وبالتالى يستهلك نسبة كبيرة من الأكسجين اللازم لأكسدة الفسفور .
ثالثاً: إزالة الكروم:
ولإزالة الكروم من المعدن المصهور يفضل توافر الظروف التالية:
- درجة حرارة منخفضة نسبيا، من 1570 وحتى 1580 مئوية وذلك لأنه تفاعل طارد للحرارة.
- خبث ذو قاعدية منخفضة نسبيا من 1.8 إلى 2.1 .
- إجراء عملية التجليخ (إزالة الخبث) باستمرار.
- خبث ذو نسبة منخفضة من السيليكا والماغنسيا (لأن السيليكون والمنجنيز لهما قابلية أعلى من الكروم في التفاعل مع الأكسجين.
رابعاً: إزالة الكبريت:
ولإزالة الكبريت من المعدن المصهور يفضل توافر الظروف التالية: درجة حرارة مرتفعة نسبياً، أعلى من 1600 مئوية، وذلك لأنه تفاعل ماص للحرارة.
- خبث ذو قاعدية مرتفعة نسبيا من 2 إلى 2.5 .
- إجراء عملية التجليخ (إزالة الخبث) باستمرار.
- توافر جو مختزل بالفرن (نسبة منخفضة من الأكسجين وال FeO)
ولذلك تتم عملية إزالة الكبريت بشكل أفضل خلال مرحلة التقنية حيث تتوافر تلك الظروف، ولكن يلاحظ أنه إذا كانت نسبة الكبريت في الشحنة المعدنية عالية نسبيا فإنه يتم إضافة كمية أعلى من الجير، أما إذا كانت الزيادة كبيرة فإننا نقوم بإضافة كمية من السيليكون والمنجنيز والكربون بغرض التفاعل مع الأكسجين وتقليل نسبته مع رفع درجة حرارة المعدن نتيجة هذه التفاعلات، وهذا كله يحسن من ظروف إزالة الكبريت من المعدن، ولإتمام عملية إزالة الكبريت من المعدن يفضل إتباع الترتيب التالى: (إجراء التجليخ ← إضافة 500كجم من الجير ← حقن الكربون مع نسبة منخفضة من الاكسجين). وعملية إزالة الكبريت تتم بشكل أكفأ خلال فرن البوتقة .
خامسأ: إزالة الكربون:
وعملية إزالة الكربون تحقق ما يلى :
- استهلاك الأكسجين وإزالته من المعدن .
- تحفيز عملية إزالة الكبريت (كما سبق بيانه).
- تكوين فقاعات من غازى ال CO وال CO2، والتي تحسن معدلات إزالة الكبريت والفسفور والهيدروجين والنيتروجين من المعدن، كما أنها تساعد على عمل تجانس حرارى وكيميائى لمصهور المعدن (عن طريق تأثير التقليب).
رابعاً مرحلة الصب (Tapping)
[عدل]وتتم عملية الصب من الفرن بعد التأكد من التركيب ودرجة الحرارة ، وذلك خلال بوتقة يتم تسخينها حتى (1000) درجة مئوية مسبقاً تحت المسخن ، هذا التسخين المسبق يحقق الأغراض التالية ..
- تجنب حدوث صدمة حرارية لمواد التبطين الحرارية للبوتقة أثناء صب المعدن .
- ضمان خلو البوتقة من الرطوبة والغازات كالأكسجين، حيث أنها قد تسبب مخاطر الانفجار ، كما تزيد من معدل تآكل حراريات البوتقة ، وتؤثر على جودة الصلب النهائي .
ويراعى الترتيب التالي أثناء مرحلة صب المعدن من الفرن إلى البوتقة :
- عمل تجليخ (إزالة للخبث من الفرن عن طريق بلب الخبث)
- التأكد من ضبط التحليل الكيميائي للمعدن ، وذلك على حسب نوع الصلب .
- التأكد من درجة حرارة المعدن بحيث تكون 1640 درجة مئوية تقريباً وتختلف هذه القيمة على حسب نوع الصلب باختلاف التركيب الكيميائي .
- التأكد من صب معدن خالي من الخبث على قدر المستطاع ، وذلك لأن الخبث يكون غني بالعناصر الغير مرغوب فيها (كالسيليكون والفسفور) وكذلك لتجنب ارتداد هذه العناصر مرة أخرى .
نبذة عن تشغيل فرن البوتقة
[عدل]فرن البوتقة هو مرحلة وسيطة بين فرن القوس الكهربي والصب المستمر ويتكون من :
- البوتقة نفسها وهي عبارة عن جسم معدني مبطن من الداخل والخارج بالطوب الحراري، وبها جزء مسامي في القاع حيث يتم ضخ الغاز الخامل من خلاله .
- ثلاث إلكترونات من الجرافيت موصلة بالتيار الكهربي .
- سقف مبرد بالماء.
- عربة لنقل البوتقة من وإلى فرن البوتقة .
ويستخدم فرن البوتقة للقيام بعمليات المعالجة الثانوية وهي :
- عمل تجانس حراري وكيميائي عبر التقليب بغاز خامل.
- إزالة كلاً من الأكسجين والكبريت.
- ضبط التحليل الكيميائي ودرجة الحرارة .
- التخلص من الشوائب الغير معدنية .

'تشغيل فرن البوتقة :' يبدأ التقليب بالأرجون ، ويبدأ عمل القوس الكهربي والذي يفضل أن يكون قصير في هذه المرحلة ، وذلك عن طريق العمل بفرق جهد متوسط ، وتبدأ عمليات المعالجة على ثلاث مراحل :
أولاً مرحلة الجلخ وفيها يتم إضافة الجير بغرض زيادة القاعدية وحماية حراريات البوتقة ، كما يتم إضافة كلا من الفلوسبار وكربيد الكالسيوم للتخلص من الأكسجين وزيادة سيولة الجلخ . ثانياً مرحلة ضبط التحليل الكيميائي عن طريق أخذ عينة من الخبث للتأكد من اختزال الحديد وحساب الإضافات المطلوبة . ثالثاً مرحلة التسخين الأساسية حيث يتم إضافة الجير وكربيد الكالسيوم ، ورفع درجة الحرارة بواسطة قوس كهربي طويل ثم يتم نقل المعدن إلى مرحلة الصب المستمر .
عملية الصب المستمر : عملية الصب المستمر هي عملية أساسية في مصانع إنتاج الصلب حيث أن أكثر من 90% من إنتاج الصلب يعتمد في إنتاجه على عملية الصب المستمر . وعملية الصب المستمر هي عملية تهدف إلى الوصول إلى منتج عالي الجودة ، وتعتمد على علم الميتالورجي بصورة أساسية .
ويمكن تلخيص عملية الصب في الخطوات الآتية :
- تنتقل البوتقة المملؤة بالصلب الفور إلى برج البوتقة الدوار .
- تدار البوتقة للتحول من مكان الاستلام إلى مكان الصب بعد تسخينها إلى درجة حرارة من 1100 إلى 1200 درجة .
- يُصْب الصلب من البوتقة الكبيرة إلى البوتقة الوسيطة من خلال صمام .
- عندما يتم مستوى الصلب المصهور في البوتقة الوسيطة إلى عمق مناسب (30 – 40 سم) يتم بدء الصب إلى قوالب الصب .
- في قالب الصب يتم عملية التجمد المبدئية بواسطة عمليات تجميد غير مباشر .
- تُسْحَبُ الكتل بعد ذلك بواسطة درافيل السحب إلى منطقة التبريد الثانوي .
- تنتقل الكتل بعد ذلك إلى وحدة القص حيث تُقَطَّع بالطول المطلوب .
- تنتقل الكتل بعد ذلك عن طريق مجموعة من الدرافيل إلى سرير التبريد حيث تُبَرَّد في الهواء.
- تُنْقَل إلى مناطق التخزين عن طريق ونش علوي
اقرأ أيضاً
[عدل]المراجع
[عدل]- ^ Pahl، Ron (2002). Breaking Away from the Textbook: Prehistory to 1600. Scarecrow Press Inc. ص. 53. ISBN:978-0810837591.
- ^ Steel Production Gas to Power, www.clarke-energy.com نسخة محفوظة 27 مارس 2016 على موقع واي باك مشين.
- الحديد والفولاذ الأستخلاص والنصنيع – الدكتور محمد عز الدهشان 1999
- Mirko, Centi; Saliceti Stefano. "Transformation Induced Plasticity (TRIP), Twinning Induced Plasticity (TWIP) and Dual-Phase (DP) Steels". Tampere University of Technology.Archived from the original on 2008-03-07.Retrieved 2007-03-01.
- "High strength low alloy steels". Schoolscience.co.uk. Retrieved 2007-08-14
- India's steel industry steps onto world stage
- Needham, Volume 4, Part 1, p. 282.
- Steel|From Wikipedia, the free encyclopedia
- Smith &Hashemi 2006, p. 363—2.08%.
- Properties of Maraging Steels
- Degarmo, Black &Kohser 2003, p. 75—2.11%.
- Ashby & Jones 1992—2.14%.
- Galvanic protection. Encyclopædia Britannica. 2007
- "Steel Industry". Retrieved 2009-07-12.
- معجزة إنزال الحديد وبأسه الشديد في القرآن الكريم والفيزياء النووية الفلكية
- Basic oxygen process. Encyclopædia Britannica. 2007
- ِAlloying of steel
- Bugayev, K.; Konovalov, Y.; Bychkov, Y.; Tretyakov, E.; Savin, Ivan V. (2001). Iron and Steel Production. The Minerva Group, Retrieved 2009-07-19.